Altair SimSolid 2022.3.0 with Tutorials & Verification (x64)
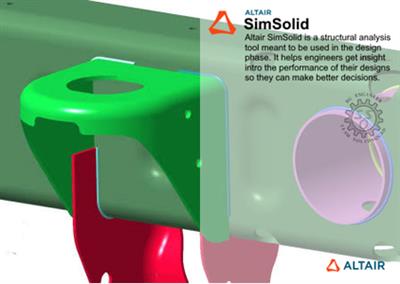
Free Download Altair SimSolid 2022.3.0 with Tutorials & Verification | 1.4 Gb
The software developer Altair is pleased to announce the availability of SimSolid 2022.3 is a structural analysis software developed specifically for rapidly evolving design processes, enabling the analysis of fully-featured CAD assemblies in minutes without meshing.
Product:Altair SimSolid
Version:2022.3 with Tutorials & Verification
Supported Architectures:x64
Website Home Page :www.altair.com
Languages Supported:english
System Requirements:Windows *
Size:1.4 Gb
Highlights
- Linux HPC support
- Squeak and Rattle
- ECAD reader
- Transient thermal-stress
- Imported thermal
- Alignment
- Virtual cable/rod
New Features
Linux HPC Support
SimSolid now supports a new platform, Red Hat Enterprise Linux. This enables running SimSolid jobs on high performance computing clusters. This is possible using batchmode scripts. All functions available in batchmode are supported on the Linux platform as well except for the import of any geometry files. The SimSolid user-interface is still not supported on Linux platforms.
Squeak and Rattle
Squeak and rattle functionality allows engineers to rapidly identify and eliminate squeak and rattle in products at an early design stage. It can be accessed by linking to transient analysis. Squeak and rattle issues can be identified by creating sampling points across the assembly and evaluating potential issues. Several responses can also be Descriptionted for more details.
ECAD reader (Beta)
SimSolid supports import of Electronics CAD files generally called ECAD files. ECAD files with extension .tgz, .tar, .zip, .pcb, .pcbdoc, .xml and .cvg are currently supported and this allows importing a number of electronics CAD files including printed circuit boards.
Transient thermal stress
Temperatures from transient thermal analysis can now be used to analyze thermal stresses and deformations. The time steps can be defined manually or imported from a .csv file.
Imported thermal
Temperatures can be imported from a .csv file to map them across the assembly. Temperature import from multiple time steps is also supported. The imported temperatures can then be coupled with structural analysis to perform thermal stress analysis.
Alignment
Alignment functionality allows for aligning contact interfaces and geometry features such as cylinders. It is enabled as a new contact condition and a boundary condition called Align under structural analysis. This functionality also allows to resolve any interference between parts.
Virtual cable/rod
A new virtual connector called Cable/Rod is now supported. Cable allows for stiffness along the rope under tension, while rod allows for stiffness along the rod for both tension and compression. The stiffness can be manually defined or set as rigid. Preloading the Cable/Rod is also supported via a boundary condition under structural analysis.
Face to surface connection
A new workflow for contact-based connections is now available via Face to surface, which allows for connection creation by picking faces in the assembly. Gap and penetration tolerances can be defined, and three levels of resolution are available.
Enhancements
Fatigue
- Fatigue events now support turning off the peak-valley compression method to account for the entire time history.
- Fatigue materials can be custom defined using fatigue solution settings that can be different from the material assigned at the design study level.
- Seam weld fatigue results are now extended to the end of the weld.
Dynamics
- Frequency functions for frequency response analysis can now include both amplitude and phase.
- The XY Descriptions now support log scale for X-axis as well.
- Extract rotations for frequency response and transient analysis.
Seam welds
- Seam weld post-processing now account for weld stresses in addition to forces. There are three responses available including normal stress perpendicular to the throat, shear stress perpendicular to the weld axis, and shear stress parallel to the weld axis.
Performance
- The performance during review and change connections has been improved.
Other
- Import of coordinate system is now supported. The import requires coordinates of three points namely the origin, a point on the X-axis and a point on the XY-plane.
- A new capability to replace missing CAD materials from the database.
- Remote point displacements are now available for remote loads.
- A new column called aspect ratio has been added to connections review that provides the ratio of the gap/penetration found at the interface to the size of the connection. This helps in identifying poor connections that cause numerical instabilities.
- Edge to surface connections don't replace existing connections in the assembly unless there is an overlap.
- Remote displacement has been re-factored to separate it out from remote load.
- Post-study can now include multi-loadcases in addition to structural analysis.
- The geometry adaptation for sheets has been improved.
- Material database has been improved to separate out the database from project materials.
- The bolt and nut tightening has been re-factored to combine both into a single boundary condition.
- The installer InstallAnywhere has been updated to 2022 R2.
- JRE has been updated to Corretto 11.0.17.8.1.
- The visualization of virtual bushings is updated to include connecting line between the origin and the connected faces.
- Virtual connectors applied to spots are now mapped in following design studies.
Updated CAD import formats

Depreciated Features
- 'Always check part overlaps on import' option in the Geometry import settings has been removed. Part overlaps check can still be accessed via the 'Check geometry defects' function.
Known Issues
- Issues with linear guide rail under virtual connectors.
- The dynamic results with base excitation defined with different functions in different directions may not account for correct transformations. This will be addressed in the upcoming hotfix.
- The remote point displacement along force direction for dynamic analysis may not account for changing directions along different frequencies.
Resolved Issues
- Improvements were completed related to elasto-plastic materials.
- Issues related to dynamic analysis results when independent functions are applied along different directions of the load.
- Numerical instabilities with sheets.
- Issues with output of velocity and acceleration phase in frequency response analysis.
- Issues importing remote loads after renaming the workbench.
- Issues reviewing results with imported remote loads.
- Issues with conversion when units of remote load are changed.
- Issues related to creating SN curve using the Estimate from UTS method.
- Issues Descriptionting rotations for datum points.
- Issues with displaying the correct units when Pick load option is used.
- Issues with thermal-stress analysis.
- Improved warning messages across different functionality.
- Issues with exporting spot welds to a .csv file.
- Issues with connections and boundary conditions when local studies are used.
- Issues with animations for frequency response analysis.
- Issues with display of bookmark names.
- Issues with folded or overlapping sheets. These regions are not treated as connected anymore.
- Issues deleting multiple points in pick info.
- Issues creating laser welds from solids.
- Issues with copied connections across design studies.
- Issues excluding seam welds from general fatigue.
- Refresh issue with display of seam weld materials.
- Issues with seam weld creation.
- Issues with capturing errors using batchmode.
- UGNX mouse setting explanation.
- Several crashes have been fixed.
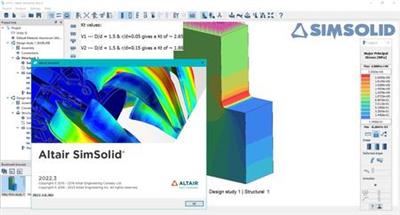
SimSolidis a game-changing simulation technology for designers and design engineers. Its just the perfect tool to kick-start any design process. This software completely eliminates the need for any geometry simplifications and meshing enabling you to get most out of your structural analysis in the least possible time. With SimSolid, model preparation is done within minutes. Even complex parts and large assemblies can be analysed with ease. SimSolid is tolerant of imprecise geometry and is just the right thing to accelerate your design process. In addition, this structural analysis solution is fast, really very fast. Highly accurate simulation results are obtained within minutes! Multiple design scenarios can be quickly analyzed and compared. And, accuracy can be specified on an individual part level allowing a rapid drill down to any level of detail that is required.
Introduction to Altair SimSolid
This video discusses some of the key benefits of Altair SimSolid and contains a detailed demo and product workflow. After viewing this video, you should be able to run your first simulation within the tool
Altairtransforms design and decision making by applying simulation, machine learning and optimization throughout product lifecycles. Our broad portfolio of simulation technology and patented units-based software licensing model enable Simulation-Driven Innovation for our customers. With more than 2,000 employees, Altair is headquartered in Troy, Michigan, USA and operates 71 offices throughout 24 countries. Altair serves more than 5,000 customers across broad industry segments.
Links are Interchangeable - Single Extraction
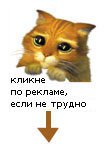